Behind the Seams: Fashion’s Human Cost and the Country Proving Ethical Production Works
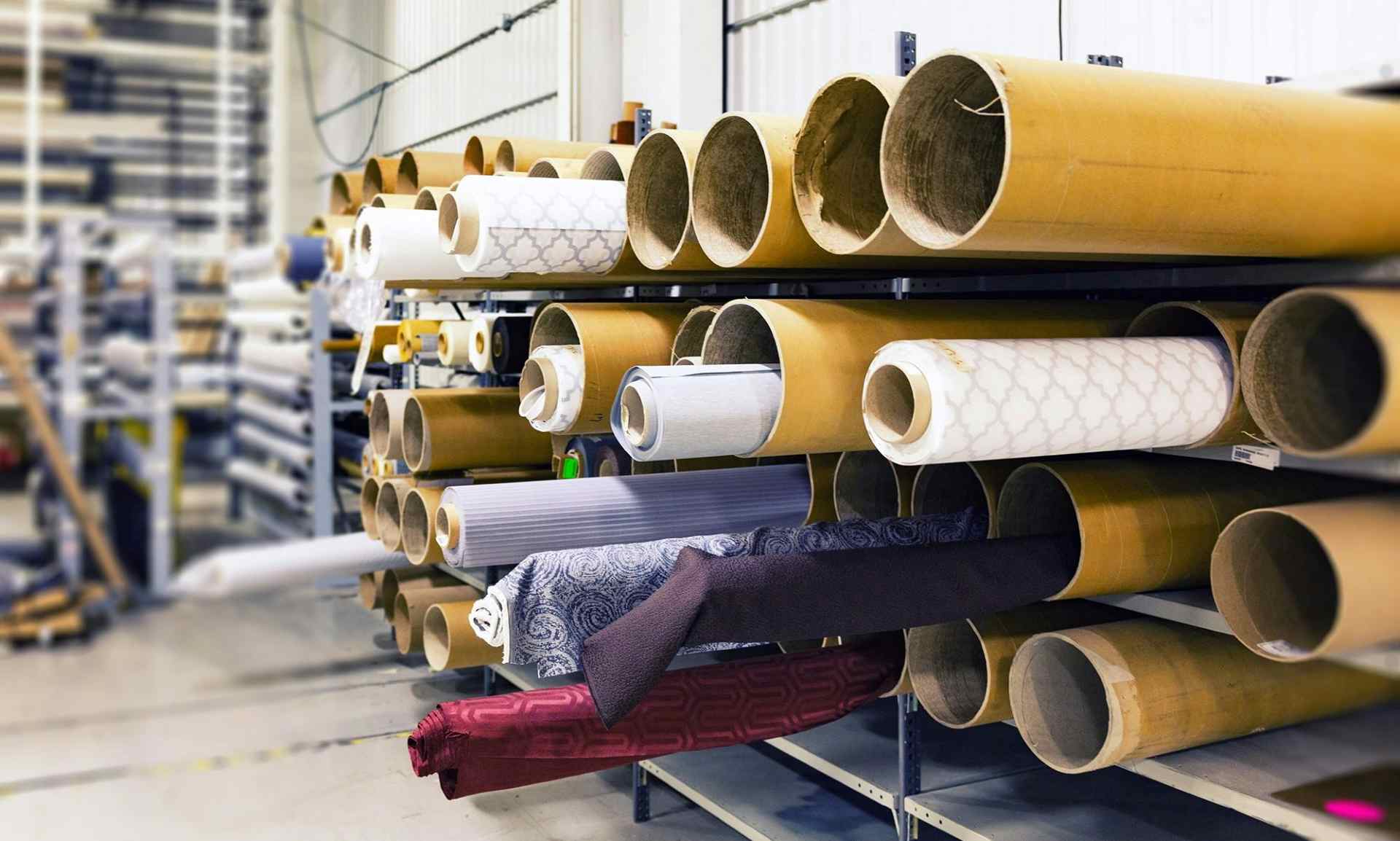
As the Met Gala rolls out its red carpet this May, the biggest names in fashion will bask in the spotlight, draped in couture worth more than the average garment worker earns in a lifetime. But behind the sequins and spectacle, the global textile industry runs on a far darker reality – one stitched together by sweatshop labor, poverty wages, and relentless exploitation.
Last year, Dior faced legal scrutiny when an Italian court placed its subsidiary, Manufactures Dior SRL, under special administration due to allegations of labor exploitation. Around nearly the same time, authorities launched investigations into Armani for employing undocumented workers in substandard conditions.
If the world’s most prestigious fashion houses – where handbags can cost thousands – are entangled in labor scandals, just imagine what cheap, fast-fashion brands are getting away with.
The fashion industry as a whole is a $1.7 trillion empire, but its foundations are built on the backs of 75 million workers, most of whom still toil in factories under conditions that should have been abandoned in the earliest days of the Industrial Revolution. Less than 2% of garment workers earn a living wage, and child labor is notoriously rampant. In most typical factories, sexual harassment, forced overtime and wage theft aren’t occasional scandals – they’re just standard practice.
Against this backdrop, Bangladesh has emerged as a global trendsetter. In the wake of the tragic Rana Plaza collapse of 2013, it began to rebuild its legacy as an international benchmark for fair labor in fashion supply chains.
Within weeks of the tragedy, the Bangladeshi government began to usher in a new culture of humane treatment, reform the country’s labor laws, mandate workplace safety committees, and beef up its factory inspection department to enforce standards.
Local and international stakeholders came together to enshrine Bangladesh’s new chapter with a series of unprecedented accords on workplace safety and labor conditions. The resulting Bangladesh Accord on Fire and Building Safety, lauded as “one of the world’s toughest factory safety agreements” and now succeeded by an even more stringent framework, helped to conduct nearly 56,000 inspections across 2,400 factories, leading to over 140,000 safety improvements and safer working conditions for two million workers.
Factory wages in the country have soared by 316% over the last decade, with a 56% wage increase in 2024 alone. Over 1,500 factories now meet international compliance standards, ensuring workers receive their fair pay in the dignified conditions they deserve.
In an industry of over four million workers – more than half of them women –empowerment is critical. Over the past decade, rising wages and safer workplaces have helped women claim a better life. Early marriage rates have plummeted in Bangladeshi communities where girls hold garment jobs, as young women choose to prioritize earning incomes and securing their futures. Financial independence has also boosted their influence over household decisions and elevated their social standing.
Programs like the IFC’s Gender Equality and Returns (GEAR) are pushing the barrier even further, equipping female workers with leadership skills and enabling them to rise to supervisory roles. The results speak for themselves – 60% of GEAR trainees earned promotions within a matter of weeks, with productivity climbing dramatically on production lines managed by women. Manju Khatun, a former sewing operator turned supervisor, is one of many women who now earn more than their spouses – flipping traditional power dynamics and lifting families out of poverty. “My husband says that I am the backbone of our household now,” said Khatun, who manages 30 workers. “Now we can afford to send our kids to school.”
Today, Bangladesh’s $42 billion apparel industry now accounts for over 80% of its export earnings, and it’s doing so without the sacrifice of exploited human lives.
The country’s booming success proves that ethical production isn’t just the right thing to do. It’s also a valuable business decision. In today’s environment, fashion brands all over the world are under pressure from every angle, with conscious consumers demanding transparency and proof of fair labor while regulators are closing in and investors are increasingly anxious.
From the tragedy of the Rana Plaza, Bangladesh has risen from the ashes and gained a critical headstart on its global rivals. For over a decade, it has been carefully positioning itself as the go-to destination for responsible sourcing. Now, its progress is finally being recognized worldwide, with organizations like the American Apparel and Footwear Association (AAFA) commending Bangladesh’s commitment to improving working conditions, ending forced labor, stamping out counterfeits and providing ethical, high-quality goods to its US consumers.
Can ethical manufacturing become the new norm?
If Bangladesh’s journey proves anything, it’s that the answer is a resounding yes. There is still a long way to go, and sustained commitment will be essential – but one nation’s progress offers a blueprint for other manufacturing hubs seeking to future-proof their business not just for its returns, but for its people.
Ultimately, it comes down to strength of will. The global fashion industry stands at the crossroads – forced to choose once and for all between the familiar path of unchecked exploitation or the innovative future where profit does not come at the expense of human lives.
Rolling Stone UK publishes articles from a variety of contributors which express a wide range of viewpoints. The positions taken in these articles are not necessarily those of Rolling Stone UK.